CNC drill chucks “High precision”
for machines with rotating cutting tools
Technical Data
concentricity (according to the test sheet |
|||||
designation | 08 | 13 | 16 | article no | |
clamping range | 0,3 - 8mm | 0,5 - 13mm | 2,5 - 16mm | Seriennummer | |
concentricity max. at a torque of |
0,03 mm * 8 Nm |
0,03 mm * 15 Nm |
0,03 mm * 15 Nm |
Ø metal bold |
concentricity |
Haltemoment at a torque of |
30 Nm ** 10 Nm |
40 Nm ** 15 Nm |
45 Nm ** 15 Nm |
Ø 3 | |
max. permissibe torque | 10 Nm | 20 Nm | 20 Nm | Ø 5 | |
holding force min. at a torque of |
80 Nm ** 20 Nm |
90 Nm ** 20 Nm |
Ø 8 | ||
max. permissing revolution | up to 35.000 RPM *** | up to 35.000 RPM *** | up tp 35.000 RPM-1 *** | Ø 10 | |
Ø 13 | |||||
Ø 16 |
* Testing of the concentricity according to test sheet “Präzision”.
** All CNC drill chucks are clamped with an Allen-T- wrench moving a bevel gear trough a bore on side of the chuck (please see instructions for use). The bevel pinion has to be actuated with a torque of 8 respectively 15 Nm to create (measured with a clean hard metal bold). Higher torques can be reached but are not necessary for normal use and have to be regarded as security in addition.
*** The CNC drill chucks are "unbalanced" suitable for work up to 7.000 revolutions per minute.
For work requiring revolutions between 7.000 and 35.000 per minute - for example alu- or wood processing - the CNC drill chucks have to be balanced along the required revolutions and balancing quality.
There are 2 types of drill chucks available:
1. dry, without coolant supply
2. central coolant supply
The CNC drill chucks can be fitted on all kinds of tool shanks.
OPERATING INSTRUCTIONS
Clamping and releasing
To guarantee a proper function of the CNC drill chucksplease follow the below mentioned instructions:
Note:
Clamping or releasing only at standstill of machine
spindle or outside the machine.
The CNC drill chuck (pos. 1) is clamped by means of
an Allen-T-wrench (pos. 3) on side of the drill chuck actuating
a bevel gear. Turn the Allen-T-wrench counter clockwise to
open the drill chuck, clockwise to close it - shown at the bore
of the bevel pinion
("+" means to close or clamp)
("-" means to open)
1st step
Open the jaw of the drill chuck wide enough to insert the
cutting tool. (pos. 2)
2nd step
Fit cutting tool (pos. 2) to the stud into the CNC drill chuck
(pos. 1) so that the tool shank is fit closely to the whole length
of the clamping jaws. (drawing 1)
Turn the Allen-T- wrench (pos. 3) clockwise to clamp the
cutting tool using the torque mentioned in the table to clamp
the tool properly. (drawing 2)
Do not use any kind of extensions for clamping. By using
a torque higher than mentioned in our table the bevel gear
can be damaged. In this case the bevel pinion will be the
rated break point to protect the drill chuck against damage.
4th step
Test the concentricity after clamping and make sure that
the tool is clamped safely.
Note:
Do not clamp the tool with tapered shafts.
5th step
The CNC drill chuck is ready for work
and can be clamped into the machine spindle.
(drawing 3)
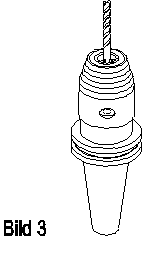
6th step
To release the cutting tool please turn the Allen-T-
wrench counter clockwise and remove the cutting tool.
Maintenance and cleaning
The CNC drill chucks are maintenance-free.The drill chucks should be cleaned after use with a clean cloth to prevent corrosion.
Before storing the drill chucks please spray oil on the surface to prevent corrosion.
Note:
Do not use compressed air to clean the drill chucks because fine chips
could get into the clamping mechanism.
Do not use any kind of solvent for cleaning because this could cause corrosion.
Repair
In case of repair please return your damaged drill chucks.To ensure full guarantee, proper function and a concentricity
of min. 0,03 mm please make use of our repair service.
By inserting the drill chuck into the machine spindle or the
magazine please follow the general instructions for use and the
safety tips of the machine manufacturer.
Guarantee according to guidelines and conditions of VDMA.
Technical changes are reserved.
Coolant supply I.K.
IK - central coolant supplyAdaption of coolant supply to the cutting tool
The CNC drill chucks use a PFTE-sealing washer between the tool and the drill chuck.To guarantee a proper sealing in the whole clamping area two sizes of
sealing washers are necessary.
Concerning 08:
The first size is for clamping ranges up to 4 mm, the second one for clamping ranges
higher than 4 mm.
Concerning 13/16:
The first size is for clamping ranges up to 6 mm, the second one for clamping ranges
higher than 6 mm.
The second size is installed in the drill chuck head, the first one is included.
Exchange of sealing washers
1st stepOpen the jaws to the biggest clamping diameter by means of the
Allen- T-wrench counter clockwise. (drawing 1)
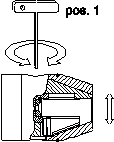
2nd step
Screw the fitting tool (pos. 1) into the sealing washer.
(drawing 2) The fitting tool is not included.
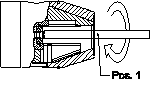
3rd step
Remove the sealing washer from the drill chuck head. (drawing 3)
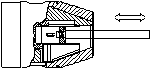
4th step
Insert the sealing washer in reverse order.
Note:
The bore of the sealing washer has to be smaller
than the coolant bore in the cutting tool.
Adaption of the coolant supply to the machine
Coolant supply according to form AD/B
The system of coolant feed allows a combination of all usual forms of coolant supply in one tool shank with form AD/B.
The system facilitates the combination of following types:
Form AD (coolant feed through a central bore)
Form B (coolant feed through the collar)
Only the positions of two set screws have to be changed in order to
adapt the CNC drill chuck to the kind of coolant feed from the machine.
These set screws (fastened with screw-locking-device low tightening)
seal the bores of the alternative coolant supply.
Basic form AD
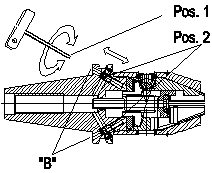
Form B
To adapt the drill chuck from the basic form to "form B" the set screws haveto be turned from pos. 2 to pos. 3 in the borehole "B" by means of an
Allen- T- Wrench SW 2,5 (pos. 1). (drawing 1)
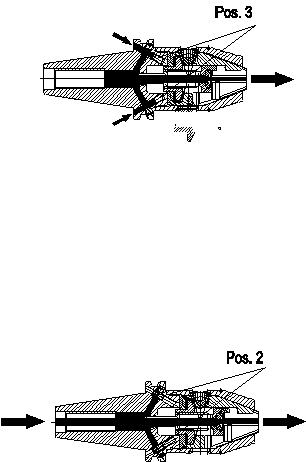
Consequently the set screws open the coolant supply through borehole "B"
whereas the coolant feed from the machine is sealed by the pull stud.